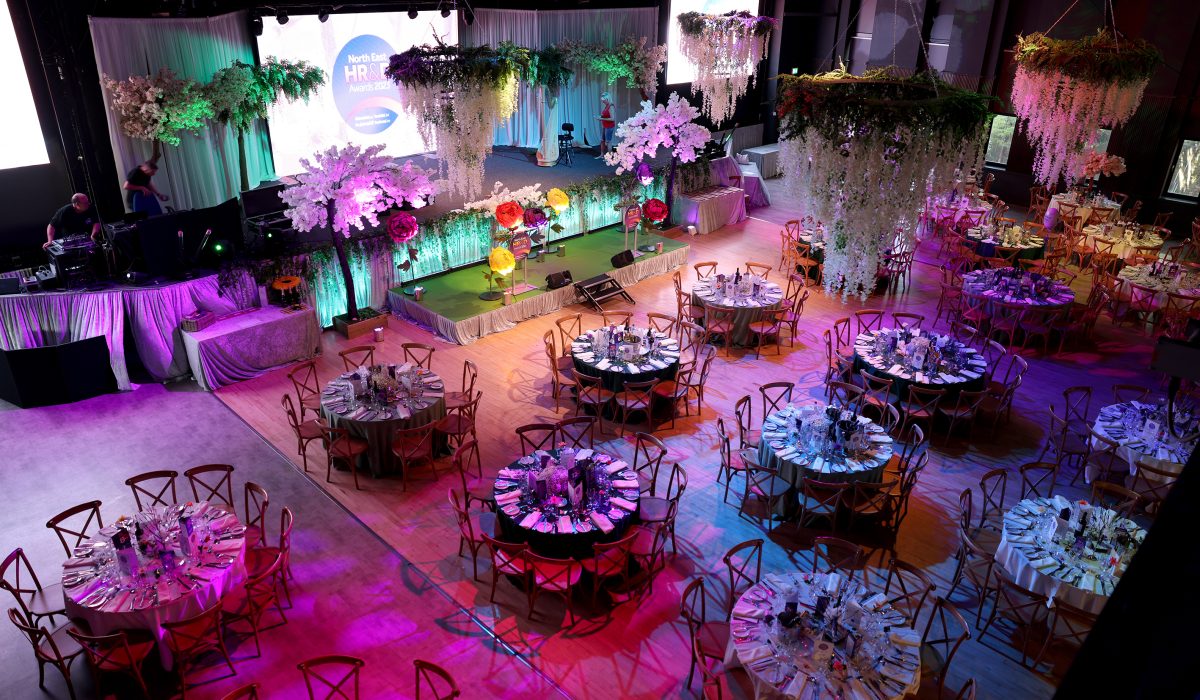
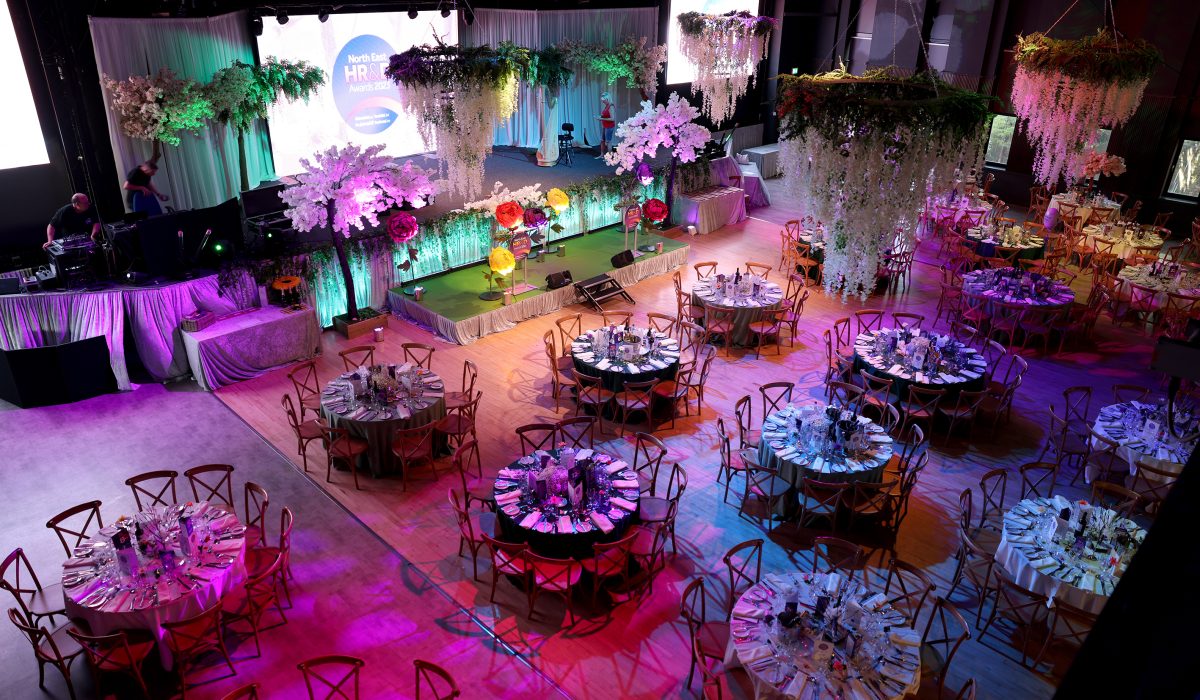
Good businesses flourish because of good people. And ensuring firms have access to the talent they need to thrive is TDR Training. Here, Steven Hugill speaks to Li Xue, the learning provider’s chief executive, and Olivia Grant and Ron Dodd, original trustees of the 25-year-old organisation, to learn more about its apprenticeship and higher education courses, and how it is working across the learning and employment sectors to catalyse engineering, manufacturing and science careers.
“People were once taught engineering and manufacturing was a dirty job, and that they’d work in a factory if they didn’t try hard at school.
“I was appalled, and I wanted to do something about it.”
Much has changed since Ron Dodd first walked British Engines’ shopfloor as a sprightly apprentice seven decades ago.
But one thing hasn’t.
While skills policy and attitudes towards engineering and manufacturing have oscillated amid Westminster short-termism, Ron has remained devoted to securing the industry’s long-term future.
And nowhere is his constancy more pronounced than TDR Training, which every year cultivates hundreds of apprentices and upskills scores of existing company staff.
“TDR was set up to make engineering and manufacturing a worthwhile career for young people,” says Ron, who worked with ex-Tyneside Training and Enterprise Council boss – and fellow original TDR trustee – Olivia Grant on its foundation.
Olivia adds: “The impetus to set up TDR came from watching the difficulties North East employers had in competing against other parts of England to secure relevant employer-led skills training.
“The passion was to give employers a lead – and as much control as possible – in getting the training they needed to face future challenges.
“And it is still the driving reason behind TDR today.”
The commitment is reflected at TDR’s Quorum Business Park headquarters, in North Tyneside, where lathes and milling machines, a recently-installed CNC machine workshop, a new welding and fabrication area and a fitting section are split into mini factory-style islands by a central walkway.
Each and all are shopfloor replicas, with intricate Batman insignias, functional bottle cap openers and a sturdy mobile phone holder immediate evidence of their use.
The apparatus, though, is matched by strong industry relations and an equally robust appraisal of workplace nuances, delivered in no small part by 25-year-old TDR’s business support services team, which tailors training needs to companies’ wants.
The result, says Li Xue, chief executive, is a unique proposition.
She says: “We provide something very different.
“Learners can undertake full-time courses at other colleges and training providers, but many are not guaranteed a job.
“We, though, find apprentices a job from day one.
“And because we own our premises, we can start them on courses all year round, as well as starting programmes in the traditional September cohort.
“We’re constantly talking to companies about learning requirements too; there isn’t presently a hydrogen power training curriculum, for example, so we’re looking to engage with businesses to create one.
“We support learners’ journeys in other ways too,” says Li of TDR, which was associate partner of the recent 2024 North East HR&D Awards and counts Komatsu, Siemens Energy and Simpsons Malt among its partner network.
She says: “We make training relevant; our machinery provides students with basic skills, but we think beyond that.
“We encourage students to be open in conversation, and allow them to document their achievements through their mobile phones, rather than a computer, because that’s what they’re most comfortable using.
“It’s a small thing, but it makes a big difference.”
Fundamental to students’ journeys is TDR’s operational model, which divides its 360-strong cohort into smaller classes to maximise learners’ exposure and sends tutors into industry to add real-time practice to its curriculum.
Li says: “We operate like a private school with classes of 16 students, which allows every learner to own a machine while on the course, and gives them more time to ask questions and understand information.
“Our tutors have dedicated development time, which means they can better shape lesson plans and participate in factory tours and experience days, to stay informed of industry changes.”
TDR’s focus spreads beyond apprentices, though, enveloping the entire education spectrum, with its teams regularly engaging with schools, to raise the engineering, manufacturing and science sectors as potential career avenues, and with firms to upskill existing staff.
Li says: “It’s our job to switch children on to career routes, and we recently welcomed three primary school teachers, who spent a full day – in overalls and boots – alongside some of our apprentices to understand their learning journey.
“Primary school teachers are mainly graduates, and we want them to see apprenticeships’ value and pass it to their pupils,” says Li of TDR, which has additionally held LEGO building and robotics competitions with youngsters.
She adds: “We’ve also seen demand increase significantly for commercial courses, across areas such as manual centre lathe (turning), CAD and CNC, electrical awareness, IET wiring regulation, MAG, TIG and Oxy welding, and people wanting to study BTEC and HNC courses to progress to a degree.
“And that has extended far beyond the North East, with mechanical and machining learners, for example, coming from London, Scotland and even Saudi Arabia.
“Some companies have to adapt quickly to the changing market environment, so they’re upskilling existing staff to move projects forward.
“And thanks to our unique offer, we’re able to help them do that.”
July 16, 2024